Discover the potential of connected Internet of Things solutions
Internet of Things (IoT) based solutions are revolutionizing machinery and industrial operations, making them more productive, safer and sustainable. Industrial IoT enables companies to connect their industrial assets and transform their data into insights. Connected IoT solutions offer industrial companies many tangible benefits from cost savings to operational efficiency, and from enhanced quality control to data-driven decision making, helping them unlock the true value of their assets.
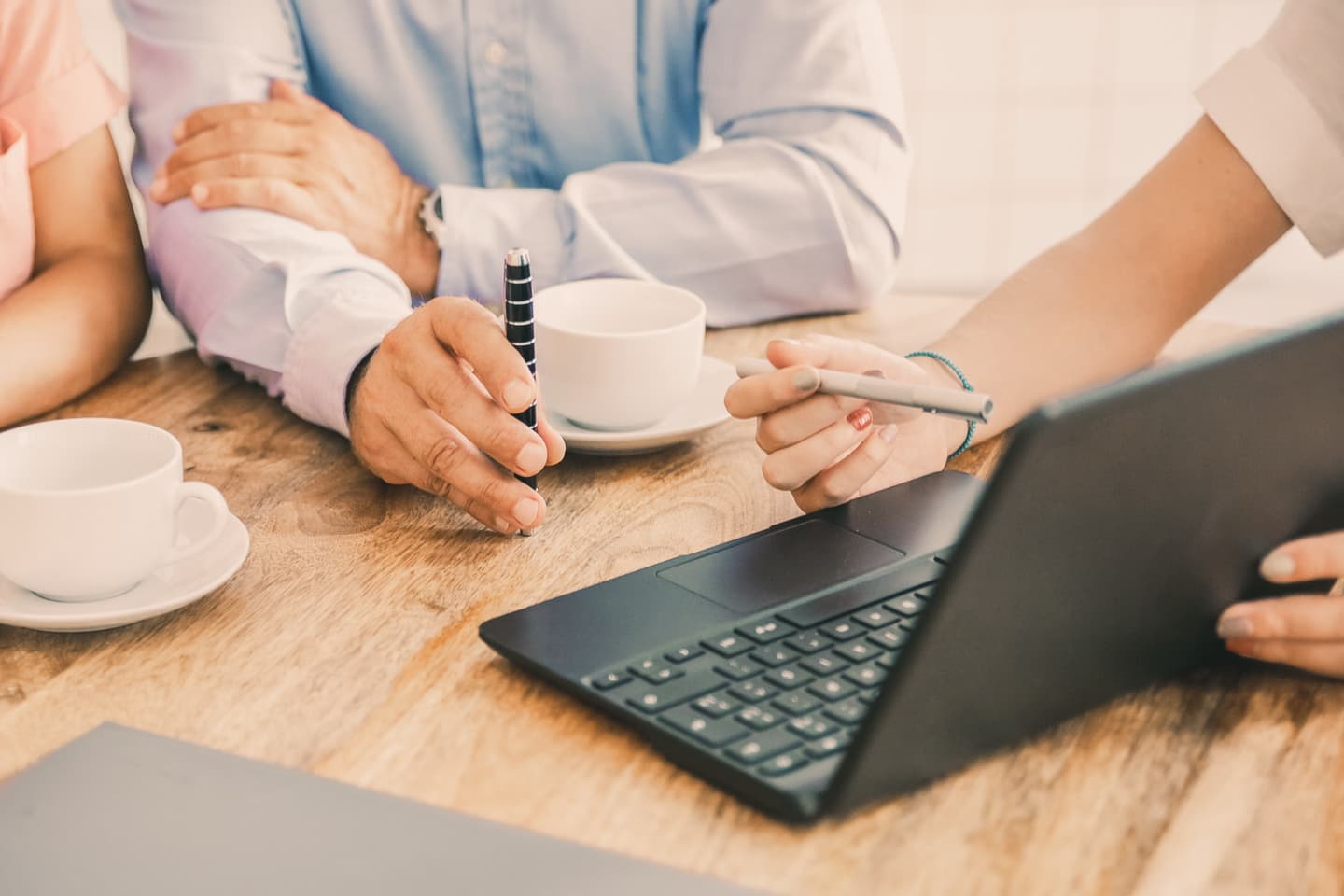
The Internet of Things has been a topic of discussion for many years, and its potential applications in machinery and industrial settings continue to expand. In this blog post, we will delve into the value generation of IoT solutions for machinery and industrial companies, providing real-world examples of their benefits and discussing areas that need further development.
What benefits do connected IoT solutions bring to the table?
Connected IoT solutions can enhance the performance of machinery and industrial companies in several ways. Using connected IoT-enabled sensors and devices, companies can collect and utilize real-time data on their machines' performance and health, enabling them to predict and address potential failures before they lead to costly downtime. When it comes to machines located in remote areas, it is particularly important to get maintenance done at the right time and have spare parts available, as dispatching parts and personnel onsite for maintenance during a breakdown might be very challenging.
Futurice has helped crane spreader manufacturer Bromma launch a spreader monitoring system, a secure and scalable cloud-based system to monitor and control a spreader’s status. It allows Bromma’s customers to remotely monitor their individual spreaders anywhere in the world, to check performance and immediately track down faults. In ports, as in any other industry, equipment uptime is a key performance indicator. Approximately 30–50 percent of a crane’s downtime is spreader related. If the spreader fails, so will the crane – generating a massive cost when loading operations stop. Bromma’s monitoring system uses data to minimize risks like these.
In another example, Fastems, a CNC solution supplier for the manufacturing industry, offers its customers the MyFastems service to have visibility of the usage of their machines, and then use the gathered data to drive productivity up.
Digital twins can help optimize operations
The concept of digital twins has gained traction over the past years and is a very promising IoT solution area. Digital twins are virtual replicas of physical assets, processes or systems, and they can be used to simulate, analyze, and optimize their real-world counterparts. Over time, they accumulate data about the system, its operation and the environment, and this data can be used to build intelligence using analytics, physics and machine learning.
In the context of IoT, digital twins can be used in conjunction with IoT-enabled sensors and devices to create a comprehensive representation of machinery, industrial facilities and operations. This allows companies to perform advanced analytics, simulate and optimize their operations, and predict potential issues before they occur. We expect digital twins to greatly increase the operational planning of various industrial processes or autonomous equipment work in cargo handling, mining and manufacturing.
What challenges exist in the IoT space
Despite promising applications, a few of which we’ve mentioned above, there are challenges and misconceptions that have to be addressed. In the following, we’ll focus on three prevalent ones – interoperability, scale, and data management.
Interoperability
One of the main problems is the lack of standardization in the IoT space. With numerous devices and platforms available, integrating them into a cohesive system can be a daunting task. Industry-wide standardization is needed to facilitate seamless integration and interoperability between different devices, platforms and vendors. This will enable industrial companies to create more cohesive and efficient IoT ecosystems.
To tackle interoperability challenges, different cloud vendors have rolled out their own software suites like the Azure IoT Hub, AWS Greengrass and Google Manufacturing Data Engine. They provide a simpler way to set up the basic infrastructure and enable their customers to focus on building custom solutions, which in turn will offer real competitive advantage.
Start small and scale up
Another challenge is the sheer (assumed) size of projects when it comes to starting to build an IoT platform. A common misconception is that you need to equip everything with connectivity and that it’ll take years to get anything concrete out before it starts generating value. But in reality, starting small is the key to success. Experiment with the part of your products where these connected services would bring most benefits and scale the solutions to cover other use cases and machines in the future.
Data management
Considering the crucial nature of data produced by various devices, it is imperative to have stringent data management strategies in place. The storage and processing of data – along with the personal information of end users – should be done in a way that prevents misuse or unintentional exposure. This should to be a consistent principle throughout the development process, helping ingrain data protection into the very fabric of the digital service.
Conclusion
To summarize, the Internet of Things has enormous untapped potential to generate value for industrial companies. By harnessing the power of connected IoT solutions and incorporating digital twins and data management, companies can significantly enhance their operations and drive productivity. With continued advancements and industry collaboration, the future for connected IoT solutions will revolutionize the way companies operate, transforming the physical world into the digital world.
Here are four key points to help you get started with connected IoT solution development:
- Define your use case: Clearly outline the objectives, scope and requirements for your IoT initiative. Identify the specific problem or opportunity you want to address with IoT, and understand the type of devices, data and actions you want to enable.
- Choose the right building blocks: Pick the appropriate IoT platform, hardware devices, and connectivity options for your project. Research and evaluate different technologies, protocols and platforms that match your needs and are sufficiently scalable.
- Start small and scale up: Build the necessary pilot environment and start collecting and analyzing data. Learn, iterate and refine your solution based on feedback and testing results.
- Capture the value: Link your solution to the operative process. Leverage data analysis for developing the business and business model.
See also: Design principles for connected devices in IoT
At Futurice, we are here to help and support you on your IoT development journey. Get in touch to learn more about how this could benefit your organization.
- Lauri AnttilaAlumni
- Liisa PaavilainenSenior Consultant, Transformation Lead